C:68® TECHNOLOGY
Our C:68® carbon achieves the impossible: lower weight and higher strength. Flat, high modulus tow spread fibres allow wall thicknesses to be reduced by up to 25%, and our Advanced Twin Mold manufacturing ensures consistency and accuracy. All you need to know is, it's an awesome material for building great bike frames.
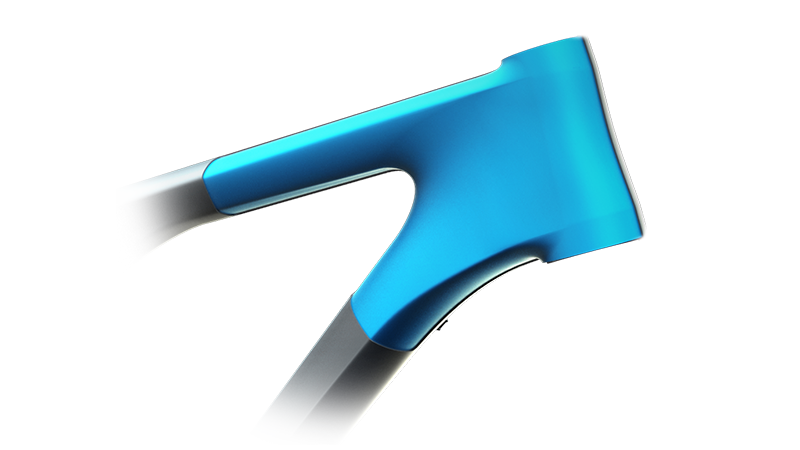
Less Resin and a Higher Fibre Content
C:68® is all about highly innovative carbon technology, less resin and a higher fibre content. A fibre content of 68% and tiny nanoparticles in the resin minimise weight while increasing stiffness at the same time.
Manufacturing process: the highly specific manufacturing process combines our Advanced Twin Mold and Zero techniques with the right materials to create the lightest carbon fibre frame on the market. Advanced Twin Mold is a special manufacturing process. We minimise imprecise overlaps by accurately fitting individual carbon layers’ overlap regions during the monocoque building process. The result is a frame with no superfluous weight – every gramme counts. We also use a solid core in the centre of the frame during the manufacturing process, which is removed when the frame is finished. This reduces the buildup of folded material and increases the safety and integrity of our lightest frames.
Zero means not bonding components to the frame unless it’s absolutely necessary. Different materials have different characteristics. Because of this, it can be risky to combine multiple materials. So we don’t use bonded aluminium components like bottom bracket shells or bearing sleeves in any of our C:68® frames. The only exception we make is for screw threads, which have to be aluminium (rather than carbon) to guarantee durability. By using this minimalist approach we save weight on the C:68® frame and mimise potential weak points – a CUBE bike should last for years!
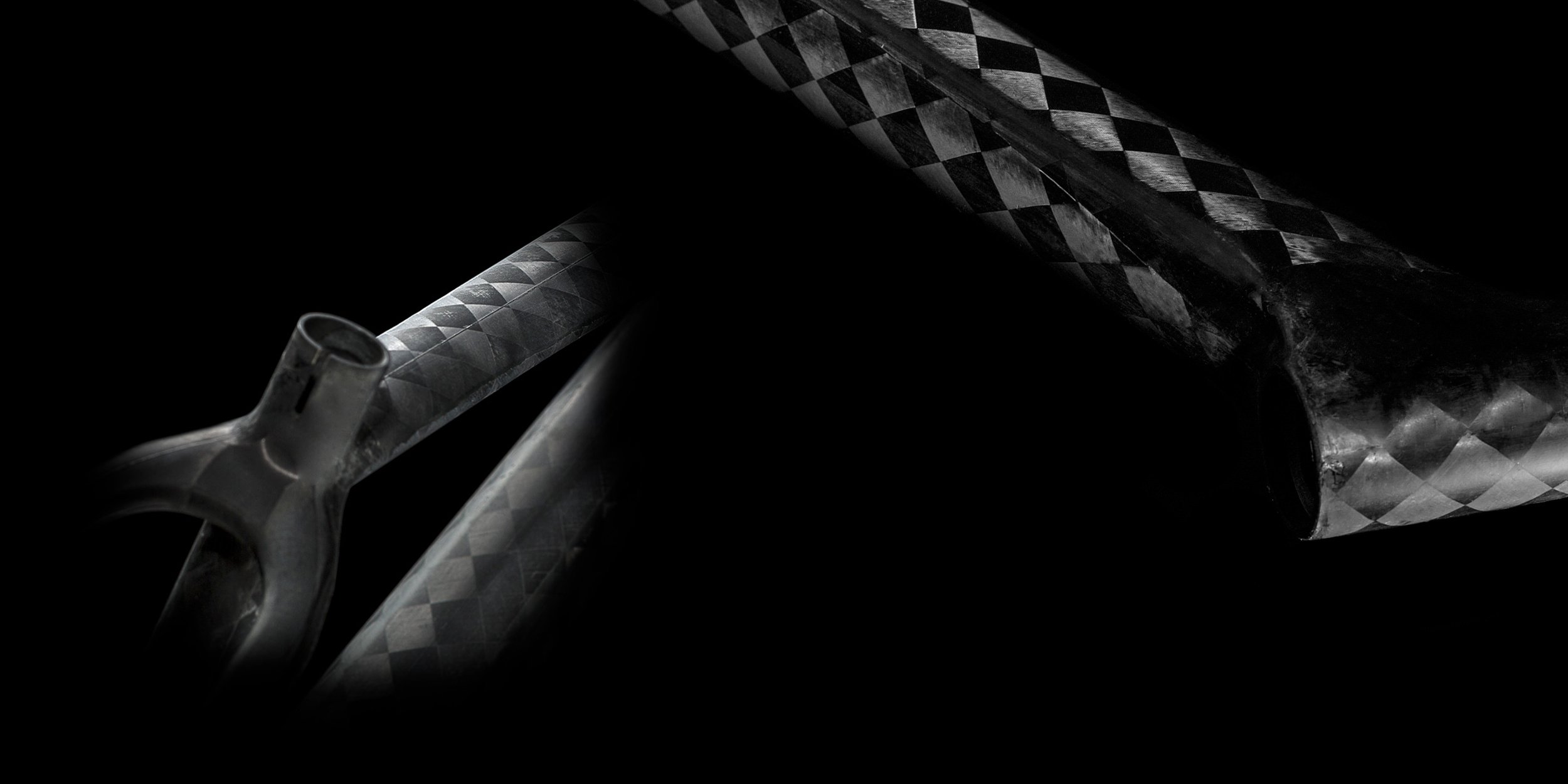
Spread Tow Material: Manufacturing Process
Materials, of course, are just as important as the manufacturing process. We can only produce our high quality C:68® carbon by using the best mix of individual ingredients. Achieving the extremely high carbon content of 68% means minimising the resin that joins the fibres together. We’ve reduced the space between fibres by applying Spread Tow Material – something that was made possible by the fibre bundles’ flat structure. These are not round, but have a stretched out cross section. This results in fewer gaps that have to be filled with resin. Because of the biaxial structure we can layer the fibres in two different directions within a single layer, allowing us to reduce wall thickness by up to 25% without compromising the stiffness or durability of the frame.
Dispersed Nano Particles: Safe and Robust
Ultra High Modulus Fibres – used until recently only in specialist applications like satellite construction - contribute to an outstanding degree of stiffness without an increase an weight. Adding precisely dispersed nano particles in the resin system improves the durability of a C:68® frame to a degree that would previously have been thought impossible. A conventional resin system can cause damage at the interface of the individual fibre layers under extreme external forces, like the kind that can occur during a crash. But the nano particles that are embedded in the resin cannot be separated by these forces. The result? The internal damage resistance – and therefore overall durability – of the frame is massively improved. It's a particularly important consideration in ultra lightweight construction, because it allows us to build a bike that's light and stiff whilst remaining safe and robust. It's the combination of High Modulus Spread Tow carbon material, evenly distributed nano particles and Ultra High Modulus fibres that produces the ultimate frame building material: C:68®.